So my coworker John (not his real name) has had some bad luck with trying to build an L-39 and has resorted to getting me to build it for him for a fee. I can't really price the time and labor on this, so I said I'd build it for him as long as he'd pray for our
adoption process. So after some discussion, he showed up at my desk one day with this:
The Eduard kit has been around for a few years and is the definitive L-39 in 1/72, and comes in various boxings. The Weekend Edition is the cheapest, with the basic kit and decals, no photoetch or resin bits. Not bad for $15 on Amazon.
Anyway John (well okay it's his real name) had occasionally asked me for tips on model building, so since I'm building this for him I'll do a step-by-step along with some techniques and some information on tools (listen up John!)
First things first - check what you need for paints. Paint colors vary widely, and in my experience the only colors that are consistent across the brands are black and white. Look at the color callouts on the instruction sheet. Sometimes you have to go match and research the colors. In this case, the color callouts use Gunze Sangyo paints, which I don't have, so I'll be matching them with Tamiya or Model master paints. You can see that I've started to scribble all over the instruction sheets.
The next thing you'll need to do is to wash the molds. Limited run kits tend to have mold release on them (some of them look like there's oil on them!), and although Eduard tends to be on the mass production side I thought the parts looked a little slick, so a quick soak for 10 minutes in warm (not hot) soapy water and a rinse should do the trick:
Next, you'll need tools. Every modeler has a basic set of tools, sometimes multiples for specific jobs. To start, you have your sprue cutters. I love my trusty
Xuron cutters, and I also have
UMM-USA's sprue cutters for cutting those delicate parts. You can see from the closeup on the UMM that they're designed to reach into tight spaces.
Next, you'll need some sanding tools. Most people have a basic emery board. I have, from left to right: sanding sticks (basically thin emery boards), a rough and smooth emery board, and a more specialized tool, a Flex-I-File, which is a sanding strip designed to sand on rounded surfaces. You don't really need a Flex-I-File, but it is convenient.
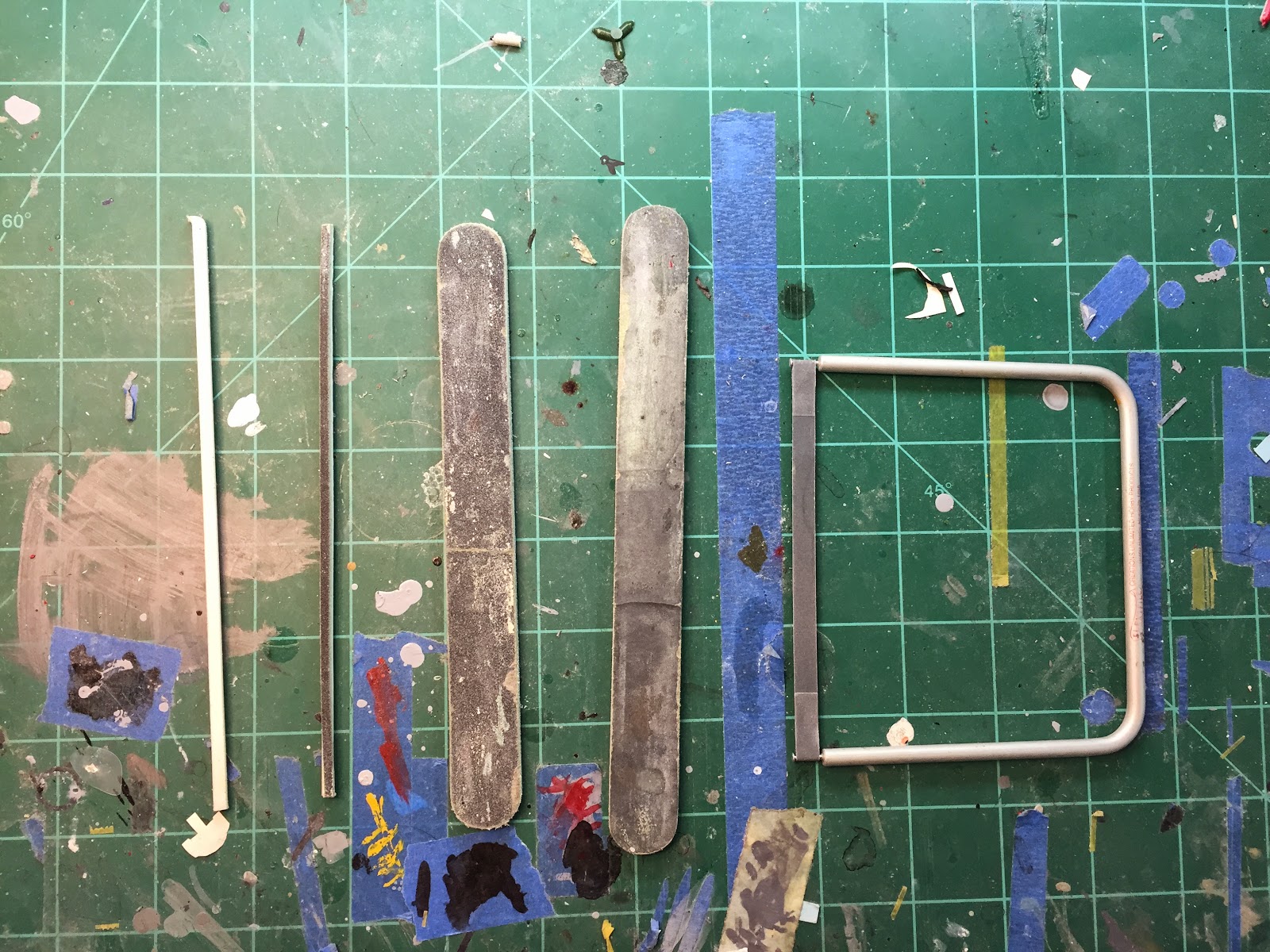
Next, glue. Most people can get away with the basic Testor's model glue. However, using specialized glues can put a model together with a lot less fuss (as long as you know what you're doing and how they're used). From left to right, Tamiya liquid cement (based on methyl-ethyl-ketone or MEK) works best for areas where you need to weld rather than glue. This stuff is pretty hot and will melt and fuse the joining surfaces together. Great for fuselage halves. In the middle is Faller Super Expert, which I've been using for years. It's similar to Testor's as it's your regular glue type, but hotter than Testor's, will go through paint, and comes with a needle applicator. Perfect for giant parts like wing joins and small parts as well. To the right is cyanoacrylate glue, aka Super Glue, which would be good for small parts that have very little surface area to attach, landing gear parts, resin and photoetch. Finally, the white tube is a recent find - jeweler's glue. It's clear, has a hypo needle applicator, perfect for clear parts!

I'll also need putty to fill seams and gaps. For the most part I use Tamiya white putty. Cures fast, sands smooth. A bit on the pricey side but well worth it. I'll also need a putty spatula (that's the thing below the putty) and a
rescriber from UMM-USA (bottom) to rescribe panel lines lost to sanding and filling - purely optional unless you're putting stuff in model competitions in which case is absolutely mandatory. Myself I don't really build for contests but I do like my models to look nice. CA glue can also be used to fill seams by the way, but I only use it for small gaps and seams.
How do I pick up those tiny parts to glue with? Not with my finger's I'm not! I use tweezers. I have two sets here: One self-clamping, and another pair of needle-nosed tweezers. Medical grade is the only way to go here.
MEK-based solvents tend to push the welded material outwards by the way, which can act as a gap filler (another reason MEK-based solvents are great since they'll automatically fill the majority of the gap with its own melted material, theoretically creating a perfect filled seam) and you may need to dispose of the excess. I tend to use this scraper to scrape the seams before sanding to finish out the surface.
And finally, you'll need a hobby knife/scalpel like an Exacto knife with a #11 blade.
Speaking of Exacto knives, sometimes the parts have some flash on them (excess plastic). This is way easier to fix than a short shot piece since it's way easier to subtract than add when it comes to material. Like this guy here - just a big chunk of excess plastic on the side of the cockpit tub. Simply carefully trim away the excess.
Once the prep work is done, the interior parts get an initial coat of paint. I did some color checking and the L-39s have a bluish gray color. I've found that Testor's Medium Gray matches fairly well, so that goes in the airbrush. The intake colors are wrong though - what Eduard wants you to do is paint the intake surfaces tan, which I thought odd. I did some research and found the intake trunking to be a dark gray. I used Tamiya's Neutral Gray, which interestingly enough turned out to be the exact shade of the plastic when the paint dried.
That was all done last night, and the paint was allowed to paint and cure overnight in preparation for a glosscoat. The glosscoat does several things: It seals the paints in, penetrates the base layer and hardens it, prepares a gloss surface for decals and also for ink/paint/oil washes. My glosscoat of choice is Pledge Floor Care Finish, formerly known as Pledge with Future (and known to modellers by its original name,
Future). It's easy to clean up, washes off with Windex, and can also be used to dip clear parts after buffing to restore a shine, impart a glass-like clarity to canopies, and finally, use it to shine your linoneum! I keep two bottles on hand - one that's for pouring out only, to be used for airbrushing and dipping, and another bottle for brushing. More details on use later.
So with Future, I brushed all the areas I just painted. Note that Future will also darken flat paints slightly. The cockpit parts and intakes have been brushed, and will be left to dry throughout the day and will be ready for decals and weathering when I get home from work (I brushed the Future on this morning when I woke up). There are two ways to apply Future, by the way - brushing or airbrush. For brush, you want to apply it in quick, outward strokes with a very clean brush (a dirty brush will deposit lint and crud on the surface). In addition, after several strokes the surface application will start to dry and become more viscous, and result in streaks that may or may not level out over time depending on temperature. I know a master modeller who does this but I haven't had too much success with this. Maybe I'll try it again sometime. The other method is with an airbrush. Pour some in and spray it out at 15psi, and patiently apply it in layers. Layer it too much and it'll pool and cause drips, layer it too little and decals will not adhere properly and silver. The trick is to layer it just enough for the surface to look glossy. I do a combination of both. For interior surfaces, I brush it, and airbrush exterior surfaces.
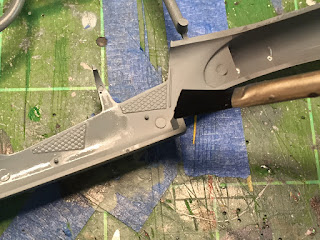
That's it for now. More updates when I get home and start on the interior bits.